Well known by mountain bikers and their extended families alike, Danny MacAskill is always dreaming up creative ideas for mind-blowing videos that reach far beyond the norm. Word on the street is that he's busy working on his next big project, and this custom carbon fiber trials bike is key to realizing his vision. It also served as a great reason for Santa Cruz Bicycles to improve upon an already industry-leading carbon frame manufacturing process.
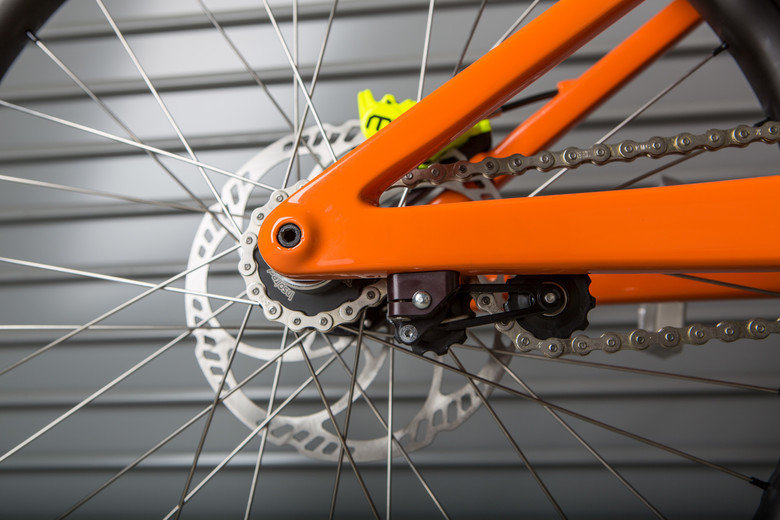
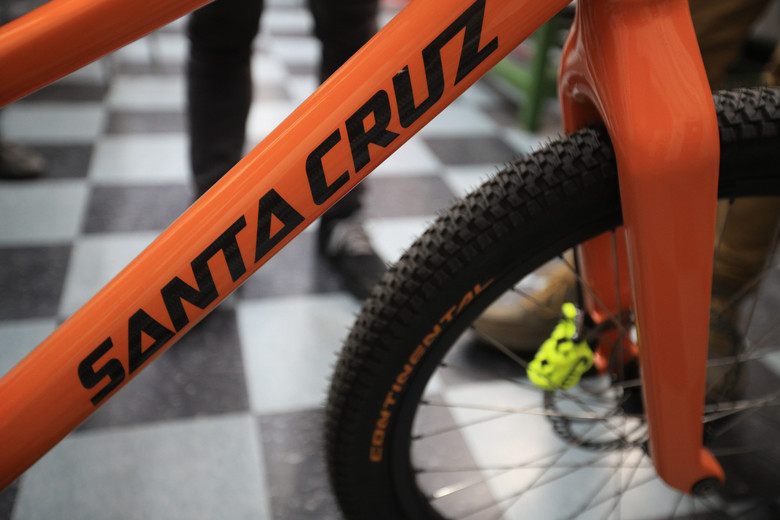
"Danny wanted us to make him a carbon trials bike. I had no idea what kind of journey that was going to be, but it sounded like there’d be a whole lot of new stuff to learn working on a project like this so I just said yes, and used it as an opportunity to take our in-house R&D facility to the next level." - Nic McCrae, Santa Cruz Composites Engineer
After experiencing firsthand what Santa Cruz could create with carbon fiber time and time again, Danny knew there was potential to do even more.
"Everything is helping me push. Riding a carbon mountain bike is helping me push my limits. Riding carbon wheels that don't actually break under me are helping me push my limits. Can you guys do a carbon trials frame for me?" - Will Ockelton, recounting Danny's remarks
Step Inside the Carbon Lab
Deep within Santa Cruz headquarters, around a few bends, down a narrow hallway, and behind closed doors, you'll find a state of the art carbon lab. Few people have the privilege to enter. Fewer still get to take photos of what's inside. It's the place where Santa Cruz developed their Reserve wheels, where custom projects for professional riders come to light, and where frames are subjected to lab tests that exceed what any human being could put them through on the trail.
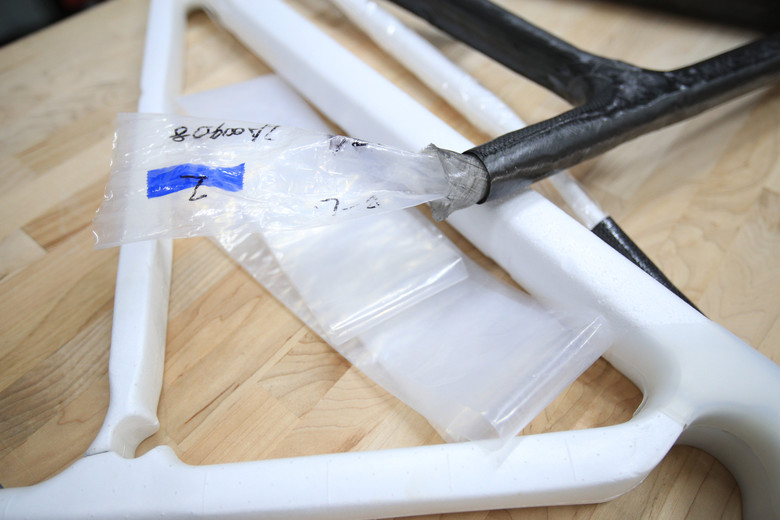

In today's production of Santa Cruz carbon frames in Asia, "manufacturing starts with an expanded polystyrene (EPS, white) mandrel wrapped in a nylon bladder. Carbon fiber plies are then wrapped around the bladder/mandrel combo according to the layup schedule, and the bladder is inflated once the frame is inside the tool."
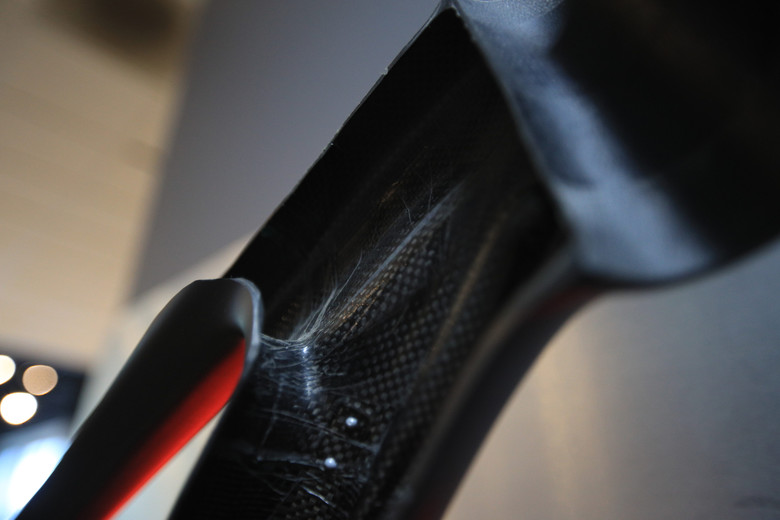
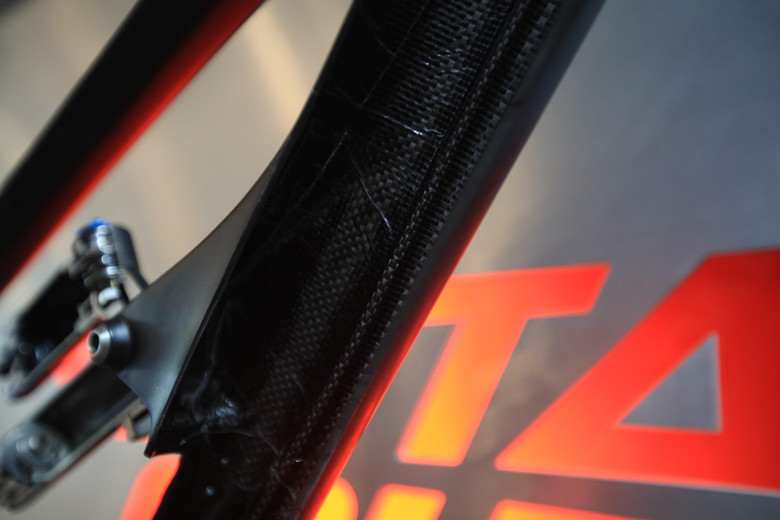
The tool (also known as a mold) is heated and the carbon cures. During the process the EPS mandrel shrinks, cracks, and is later removed with the nylon bladder and both are discarded. An example of the resulting insides of a frame is shown above. See the small ridges? Though it's pretty common practice today, Santa Cruz says they developed the first bikes that used this process back in 2009 with the Blur XC.
Danny's bike is different, not only because it was made in California, but more importantly because of how it was made. In an effort to make the process more sustainable, more adaptable, and the end product more consistent, Santa Cruz has developed a new manufacturing method they seem keen on implementing in their Asia production facilities in the future.
Rather than using EPS mandrels that are made through injection into steel molds, Santa Cruz has co-developed a 3D mandrel printing process. These 3D prints are then dipped into liquid latex and used to make latex bladders – something no one else is doing. "Reusable latex bladders are used in a variety of non-bike manufacturing environments," Santa Cruz notes, "but they typically require CNC-machining an aluminum mandrel to dip into the liquid latex, and each mandrel can take around 100 hours to machine."
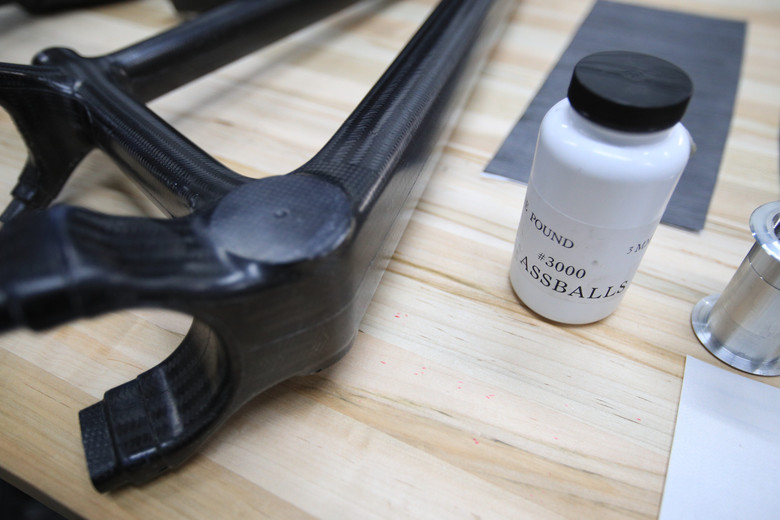
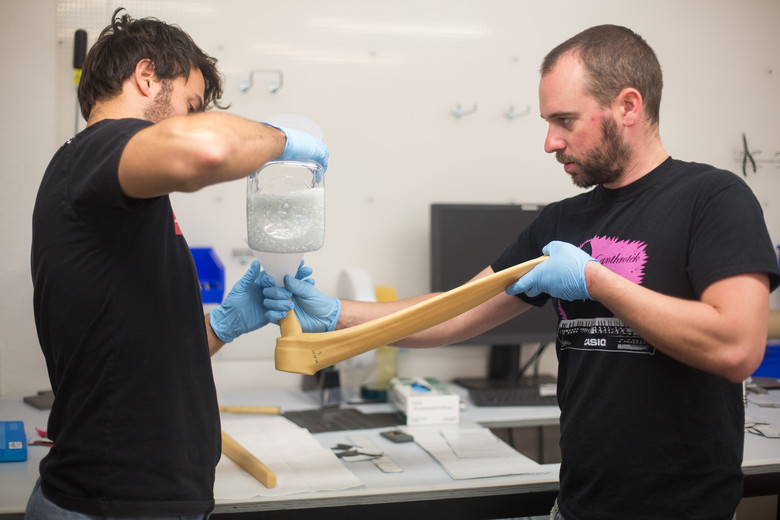
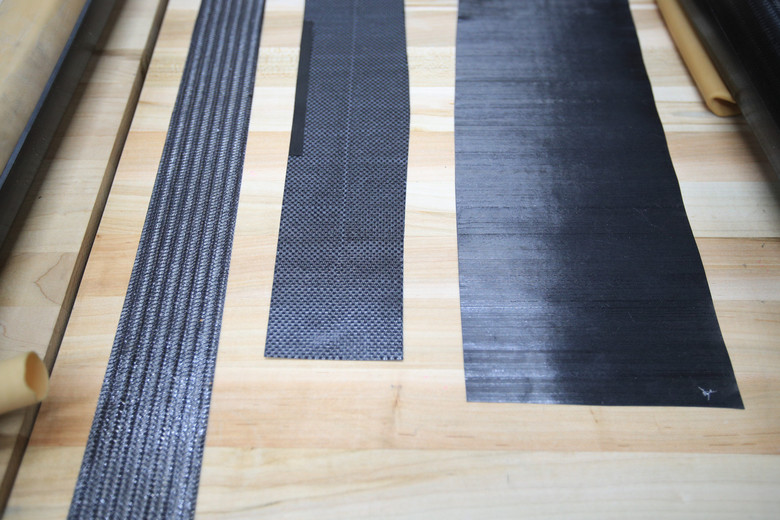
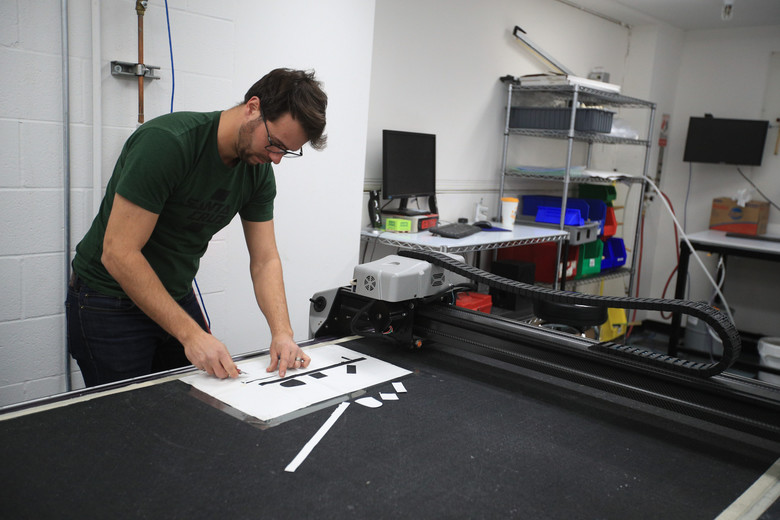
Each latex bladder is then filled with glass beads and a vacuum is applied, making the bladders rigid so they can be wrapped with carbon plies. Once the carbon is layed up, the vacuum is removed, the glass beads drained, and the wrapped bladder is placed inside the mold.
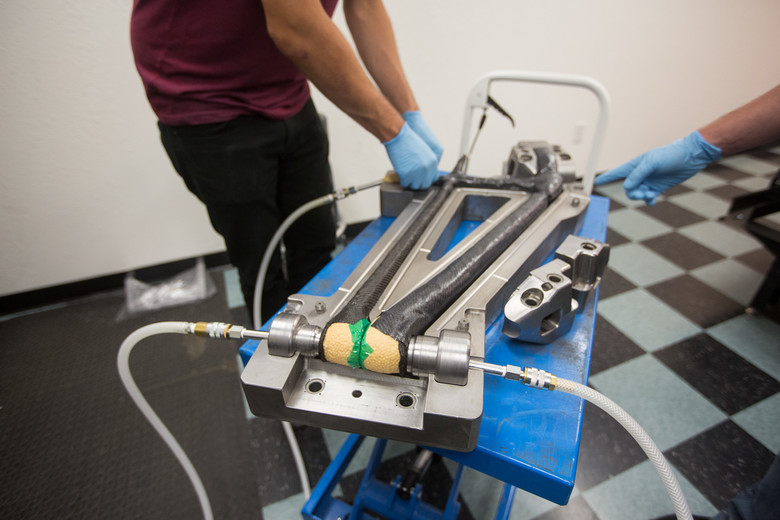
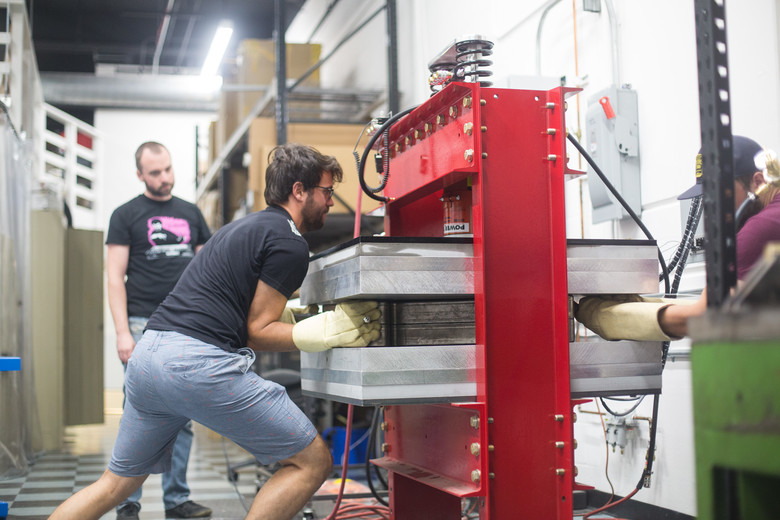
Once in the mold, it's placed into a custom heat press and the bladder is pressurized to 150psi to push the carbon outward while it's heated and cures. Afterward, the latex bladder is pulled out of the frame and the individual frame pieces are bonded together as needed.
Unlike EPS, the latex bladder can be reused up to fifty times. "Some bike frames are made using latex-dipped EPS mandrels," noted Santa Cruz about other manufacturing techniques, "but those bladders are still one-time use."
Latex is also very stretchy, unlike nylon bladders, so it can mold to the inside of the frame much better. This makes the end product incredibly smooth inside, eliminating folds, lines, and creases for more uniform walls and presumably a stronger frame.
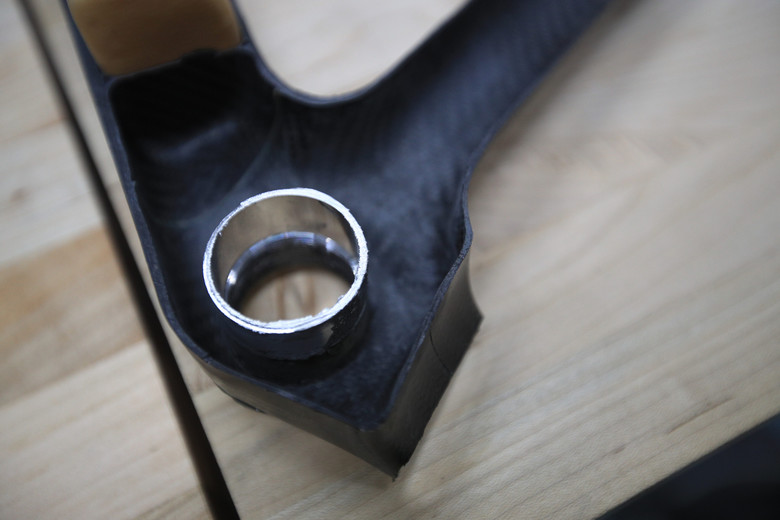
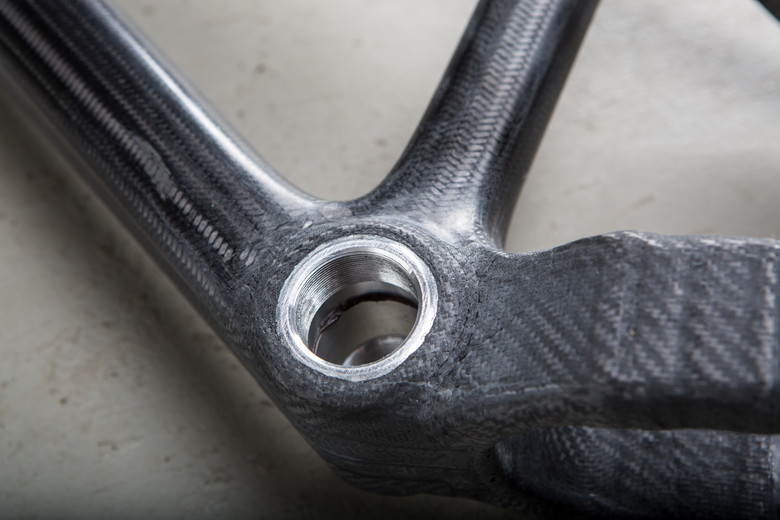
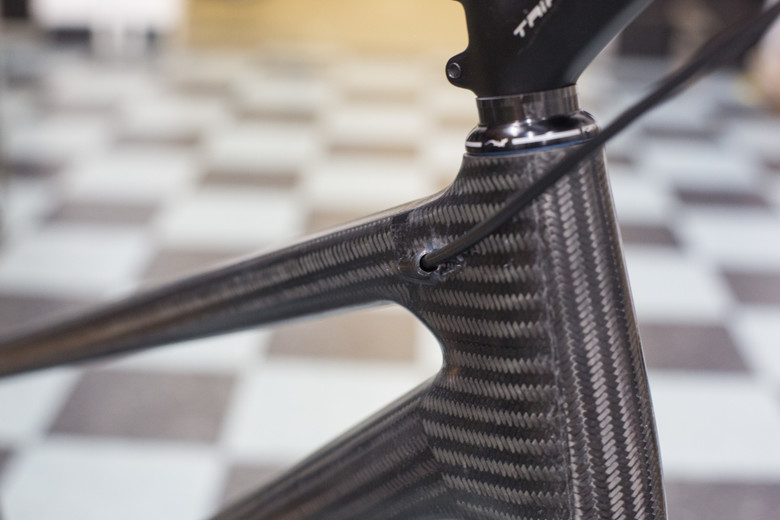
Should changes be needed to the frame, say to make it stronger in a certain location, a new 3D mandrel can be printed overnight to make room for more material inside the frame with no need for a new mold. At least three sets of mandrels and bladders were made before arriving at Danny's final frame.
Bike Check with Danny
Danny's full carbon dream bike sports custom 24-inch Reserve carbon wheels and a hint of some very special, Department of Defense controlled, impact-resistant braided carbon coming through the lettering on the downtube.
The frame is the result of thousands of man hours, lessons learned through over a dozen prototypes, and the vision of some talented engineers and designers. It's also the single most expensive thing Santa Cruz has ever made. Then again, the new manufacturing process is likely to change the game once again when it's used to make production carbon bike frames in the years to come.
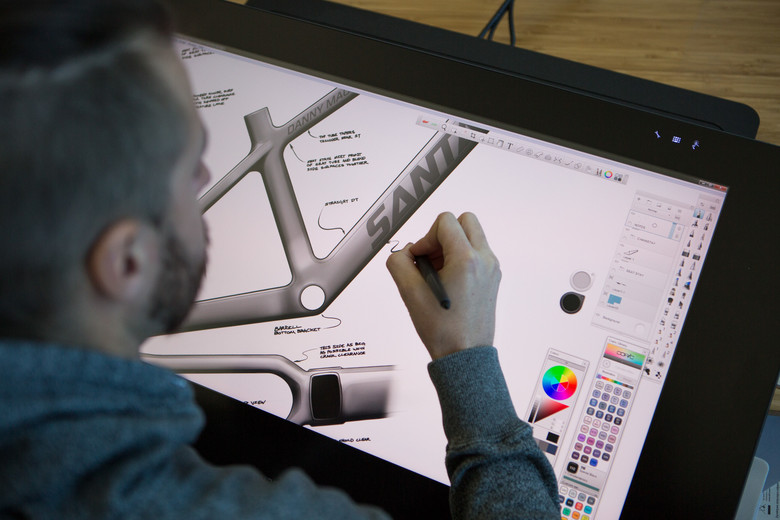
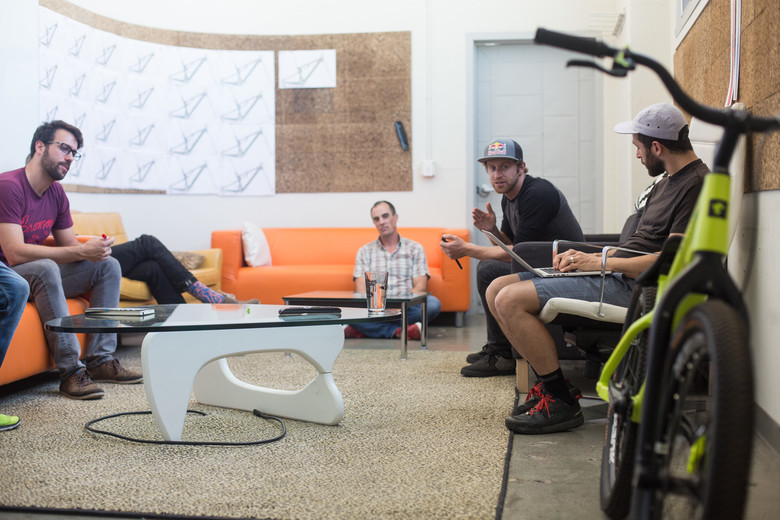
What is Danny's next major project? With four pounds less weight to throw around, we can only imagine the absolutely crazy moves we're sure to see...
Visit www.santacruzbicycles.com for more details, including some behind the scenes testing and an entertaining story about the time one of Danny's prototypes ended up inside a house oven.
Photos by Gary Perkin, Nic McCrae, and Santa Cruz
View replies to: Danny MacAskill's Custom Trials Bike Represents the Future of Carbon for Santa Cruz
Comments